In order to improve the fatigue strength of crankshafts, many crankshaft production plants use gas nitrocarburizing technology (gas nitrocarburizing is a chemical heat treatment process developed by liquid soft nitriding, which is essentially low temperature carbon based on nitriding. Nitrogen eutectic. It is characterized by low processing temperature, short time, small deformation of workpiece, stable quality, and is not limited by steel type. It can significantly improve the wear resistance, fatigue strength, anti-seizure and anti-scratch properties of parts. It can also solve the toxicity problem in liquid soft nitriding, avoid public hazard and thus have good working conditions. In addition, the equipment and operation are simple and easy to popularize. The basic principle is that the principle of gas nitrocarburizing is 530 ° ~ 580 ° C 2CO→[C]+CO_2 (carburizing) and 2NH3→2[N]+3H_2 (nitriding) reaction are generated in the atmosphere to form nitride or carbonitride on the steel surface.) The general factory, Weifang Diesel Engine Factory and Heavy Duty Truck Group Fuqiang Power Company are typical representatives. Only Shandong Crankshaft General Plant has nearly 10 sets of continuous soft nitriding production equipment and 5-2 gas soft nitriding equipment. The equipment capacity of the heavy-duty truck Group Fuqiang Power Company has reached the most advanced technology, the largest power, and the largest amount of furnace loading. At the same time, it has more energy-saving and environmental protection effects than the equipment in the same industry.
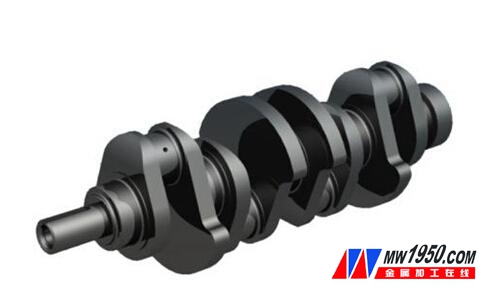
At present, the typical materials used in domestic production of crankshafts are 45 steel and 42CrMoTi.
Crankshaft gas soft nitriding is similar to other soft nitriding parts. The nitriding process generally involves five stages, including pre-cleaning, heating, heat preservation, cooling, and post-cleaning, including the furnace. Different manufacturers have slightly different gas softening processes.
1. Front cleaning process
The parts to be treated should be cleaned and oil-free by cleaning before charging. The main cleaning methods currently used are as follows: high-temperature steam plus cleaning agent and then high-temperature steam washing, automatic cleaning, and gasoline scrubbing.
The quality of the cleaning will directly affect the processing quality of the crankshaft and prolong the processing cycle. If the surface of the crankshaft is dirty, the surface of the treated crankshaft is covered with a lot of carbon black, which affects both the appearance of the product and the quality of the product. After the improved cleaning process, the quality of the treatment is greatly improved. According to practical experience, surface cleaning tends to form a continuous layer of compound having a relatively uniform thickness, and conversely, it is difficult to form a continuous and uniform thickness of the compound layer. In the case of gas soft nitriding, the compound layer contributes a lot to hardness, wear resistance and fatigue resistance. The third way of this paper is a workaround when production conditions are not available, only for small-scale cleaning.
2. Pre-oxidation process
In order to ensure the comprehensive requirements of the performance of the parts, pre-heat treatment is generally required before the gas soft nitriding. The preheating temperature of the gas nitrocarburizing is generally 400-490 ° C, and the temperature is kept for about 1 h to remove the oil stain and grease on the surface of the workpiece. A layer of oxide is formed to slowly form the (alloy) nitride to make the deep layer more uniform. According to the degree of deformation of the part, the appropriate heating rate is selected and the structure should be sufficiently homogenized in the prior heat treatment.
3. Soft nitriding process
The gas soft nitriding process parameters are generally: average heating rate 100 ° C / h; holding temperature is 540 ~ 570 ° C; holding time is 3 ~ 4h.
(1) Selection range and control of soft nitriding temperature
For carbon steel or cast iron or low alloy steel, gas soft nitriding (low temperature carbon, nitrogen osmosis) technology is often used. A lot of practice shows that the hardness and permeability of the nitride layer have an extreme relationship with temperature, time and concentration. In the ternary phase diagram of iron, nitrogen and carbon, the allotropic transition point is slightly reduced, and its isothermal section is reduced to approximately 575 °C. When the temperature is higher than 575 °C, the layer and hardness decrease rapidly with the increase of temperature. When the temperature is higher than 600 °C, the layer disappears almost completely. In order to have a good carbon and nitrogen co-infiltration effect, the control temperature of gas nitrocarburizing is generally 570 ° C (higher than the ternary eutectoid point). Nitrogen-containing austenite is formed in the surface layer, and nitrogen-containing martensite is formed upon rapid cooling to form a high hardness on the surface, so that soft nitriding is easy to adopt rapid cooling. In the early stage of soft nitriding (about 3h), it is a strong infiltration stage, forming a high nitrogen potential phase ε in the surface layer, increasing the osmotic velocity, and then entering the diffusion stage, reducing the surface nitrogen content and reducing the brittleness.
(2) Proportional flow rate of soft nitriding process gas
The ratio of NH3, CO2, and N2 during strong infiltration is generally 55:5:40, and the ventilation is generally 1.5 to 2 times the volume of the furnace. Appropriate increase of NH3 content can improve the seepage layer; appropriate increase of CO2 content can improve the surface hardness of the workpiece (if HV10 measurement, the factors affecting the surface hardness are nitrogen front matrix hardness, diffusion layer depth, white bright layer hardness. 45 steel requirements The hardness of the nitrogen precursor should be >200 HBW). The ratio of NH3, CO2, and N2 during diffusion is generally 40:5:55, and the amount of ventilation is generally 1 to 1.5 times the volume of the furnace.
The hydrogen content in the furnace: the hydrogen content in the strong osmosis zone is 10%~18% (the hydrogen content of the new furnace is low); the hydrogen content in the diffusion zone is 8%~13% (the hydrogen content of the new furnace is low).
Oven process: Each time before the new furnace is loaded, the osmosis should be carried out. The osmosis time is 6~12h, and the hydrogen content is more than 10%. After a new furnace has been used for a period of time (3 months), it should be emptied. The temperature is kept at 600 ° C for more than 12 h, only a small amount of nitrogen is passed, and the optimum hardness and permeability can be obtained by maintaining the furnace pressure (240-300 Pa).
4. Soft nitriding and cooling process
In order to make the crankshaft have better carbon and nitrogen co-infiltration effect, the control temperature of gas nitrocarburizing generally takes 570 ° C (higher than ternary eutectoid point) to form nitrogen-containing austenite in the surface layer, and forms rapidly after nitriding. Nitrogen-containing martensite makes the surface quickly form a high hardness, so soft nitriding is easy to adopt rapid cooling. The continuous soft nitriding cooling of a certain equipment manufacturer adopts oil cooling, and the equipment adopts completely automatic control. The pushing mechanism directly pushes from the nitriding furnace body to the oil cooling lifting platform, and automatically drops to the oil tank cooling. The cooling is cooled by double stirring, and the stirring is generally fast: 5-6 min, 1300 r/min. Slowly stir: about 10min, 750r/min. Take the oil for about 5 minutes. After cooling, the crankshaft will be deformed in size. As long as the deformation is well treated (2~4h), the uniform temperature rise can ensure the deformation is small. The Weibo diesel engine plant's nitriding crankshaft axial runout control is better.
5. Nitriding cleaning process
After processing, the parts should be cleaned and oil-free by cleaning. The main cleaning methods currently used are as follows: high-temperature steam plus cleaning agent and then high-temperature steam washing; automatic cleaning machine cleaning; gasoline scrubbing.
Led Mirror Cabinet
Product Feature
Quick installation unit for Mirror Cabinet
Suitable uses for different style of bathroom and indoor decoration
Details
After-sale Service: Online technical support
Project Solution Capability: total solution for projects
Application: Hotel, Hotel Home Bathroom Decoration
Design Style: Modern
Place of Origin: Guangdong, China
Brand Name: Duraplex
Style:Modern
Type: Mirror Cabinet
Shape:Rectangle
Product Name:Bathroom Mirror Cabinet
Size: Can be customized
Certificate: ETL, SAA, CE
led mirror with cabinet, smart led mirror cabinet, led bathroom mirror cabinet, led mirror cabinet bedroom, aluminium led mirror cabinet
Duraplex Limited , https://www.fsduraplex.com