The CNC rotary table can be used to achieve a circular feed motion. In addition to the circular feed motion, the CNC rotary table (referred to as the CNC rotary table) can also complete the indexing movement. The function of the indexing table is only to change the surface of the workpiece, and it can be used together with the automatic tool changing device to realize the multiple installations of several surfaces in one installation of the workpiece, thus greatly improving the working efficiency. The shape of the CNC turntable and the indexing table are not much different, but there are a series of features in the structure. Since the CNC rotary table can realize the feed motion, it has much in common with the feed drive mechanism of the CNC machine. The difference is that the drive mechanism realizes the linear feed motion, and the CNC rotary table realizes the circular feed motion.
The rotary table is widely used in various CNC milling machines, boring machines, various vertical cranes, and vertical milling machines. In addition to requiring the rotary table to withstand the weight of the workpiece well, it is also necessary to ensure its rotation accuracy under load. The rotary table bearing, as the core component of the turntable, not only has a high load carrying capacity during the operation of the turntable, but also needs to have high rotation precision, high anti-overturning capability, and high rotational speed capability. In the design of the rotary table, the types of bearings used are roughly divided into several types:
Thrust ball bearing + cylindrical roller bearing
Thrust ball bearings can withstand certain axial forces, so the bearings are mainly used to bear the weight of the workpiece; cylindrical roller bearings are mainly used for radial positioning and external radial forces (such as cutting force, milling force, etc.) . This type of design is widely used and relatively inexpensive. Since the thrust ball is a point contact bearing, its axial bearing capacity is relatively limited, and it is mainly used in small or medium-sized machine tool rotary table. In addition, the lubrication of the thrust ball is also difficult.
Hydrostatic bearing + precision cylindrical roller bearing
The hydrostatic bearing is a sliding bearing that supplies pressure oil externally and establishes a static pressure bearing oil film in the bearing to achieve liquid lubrication. Hydrostatic bearing always works under liquid lubrication from start to stop, so there is no wear, long service life and low starting power. In addition, this bearing also has the advantages of high rotation precision, large oil film stiffness, and can suppress oil film oscillation. Precision cylindrical roller bearings have good radial bearing capacity, and thanks to the use of precision-grade bearings, the rotary table's rotation accuracy is also well guaranteed. Rotary tables designed with this type can withstand high axial forces, some of which weigh more than 200 tons and have a turntable diameter of more than 10 meters. However, this type of design also has some shortcomings. Since the hydrostatic bearing must be supplied with a special oil supply system to supply the pressure oil, the maintenance is complicated and the cost is relatively high.
Crossed roller bearing
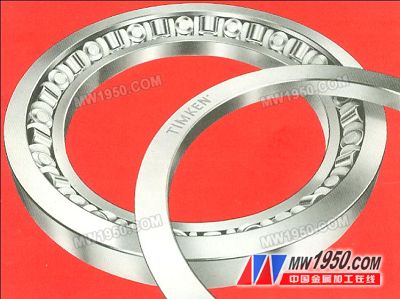
Figure 7. Crossed roller bearing
Cross roller bearings (see Figure 7) are also commonly used on turntables. Crossed roller bearings are characterized by two raceways in the bearing and two rows of rollers arranged in a row. Compared to conventional thrust bearing + radial centering bearing combinations (see Figure 8), the cross roller bearing is compact, compact and simplifies the table design, reducing the cost of the turret.
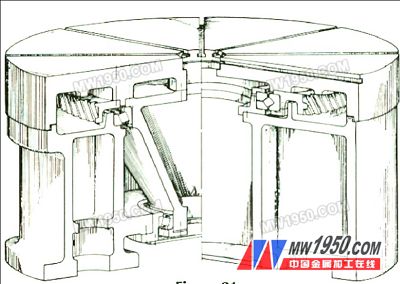
Figure 8. Comparison of turntable design between crossed roller bearings and conventional bearings
Previous page | 1 | 2 | 3 | 4 | 5 | Next page |
In the age of the energy shortage, micro duct and cluster tube low cost and high quality has obvious advantages, by the telecommunication operators and highway investors, in recent years has been widely used in Europe and America, has been called the fourth generation communication pipeline products.
Product features:
1.reliable quality guarantee
2.flexible convenient network scheme
3.safe and fast laying cable way
4.Improve the resource utilization of existing pipeline
5.the best choice of Super capacity installment construction information channel
Product advantage:
1.material cost and construction costs are far less than The same number of silicone core tube
2.according to the market demand stage investment, Avoid optical fiber assembly density , improve underground pipeline resources;
3.Elastic expansion ability, meet sudden demand of optical fiber communication service.
4.construction simple, greatly shorten the construction period
5.compatible with existing optical fiber, adapt to the market development, technology stay on top.
6.Micro duct main performance indexes cluster tube core pipe
7.maximum traction's load (N) ≥3500 ≥300
8.tensile strength (Mpa) ≥15 ≥18
9.Breaking elongation rate (%)≥350 ≥500
2, cluster pipe : one or a few micro ducts, According to certain permutation order together , topical, PE sheathed layer, the products made of cluster, In the limited space in can accommodate more pipeline quantity
.
Structure features:
Through the color code, every micro ducts are defined in the cluster root the position of the tube , and convenient for construction, effectively avoid microtubules fault;
through special process and product formula, to ensure the micro ducts and the sheath layer relative separation, convenient for construction and the connection of internal micro ducts
through the cluster management layer color is different, or in the cluster tube sheath layer increased stripe logo to distinguish the mocro ducys in same the trench.
Technical Specifications for Micro Duct:
S.No.
|
Parameter
|
Specification / Tolerance
|
1
|
Density
|
0.940 to 0.958 g/cc at 27ºC
|
2
|
Melt Flow Rate
|
0.2 to 1.10 gm /10 Minute at 190ºC & 5 kg load
|
3
|
Minimum Bend Radius
|
No cracking, splitting, breaking or permanent reduction in diameter when bend to 180º at radius of 10 times the diameter
|
4
|
Internal Pressure Test
|
5 Minutes at 27ºC & Induced stress at 3.8 mpa.
|
5.
|
Internal Coefficient of friction
|
Max 0.1 at 6.8 Kg load
|
Dimensions (in mm) of Silicoat PE Micro Duct :
Nominal Size
|
Outer Diamter
|
Wall Thickness
|
Inner Layer Wall Thickness
|
Ovality
|
OD
|
ID
|
MIN
|
MAX
|
MIN
|
MAX
|
MIN
|
7.0
|
5.5
|
6.9
|
7.1
|
0.65
|
0.75
|
0.10
|
0.20
|
10.0
|
5.5
|
9.9
|
10.1
|
2.15
|
2.25
|
0.10
|
0.20
|
10.0
|
8.0
|
9.9
|
10.1
|
0.9
|
1.0
|
0.10
|
0.20
|
10.0
|
7.6
|
9.9
|
10.1
|
1.1
|
1.2
|
0.10
|
0.20
|
12.0
|
8.0
|
11.9
|
12.1
|
1.90
|
2.10
|
0.10
|
0.20
|
12.0
|
9.6
|
11.9
|
12.1
|
0.90
|
1.0
|
0.10
|
0.20
|
Note * 14/10 mm size also available
|
Type and Dimension Deviation of Micro-duct Bundle:
Unit: mm
Type
|
Description
|
OD
(Reference)
|
Wall Thickness
|
Deviation of Wall Thickness
|
MDB-5/3.5-7
|
7holes 5/3.5mm Micro Duct Bundle
|
20.4
|
2.7
|
-0.2, +0.2
|
MDB-7/5.5-7
|
7holes 7/5.5mm Micro Duct Bundle
|
27
|
3.0
|
-0.25, +0.25
|
MDB-10/8-7
|
7holes 10/8mm Micro Duct Bundle
|
34.4
|
2.2
|
-0.2, +0.2
|
MDB-12/10-1
|
1holes12/10mm Micro Duct Bundle
|
21
|
4.5
|
-0.3, +0.3
|
MDB-12/10-4
|
4holes12/10mm Micro Duct Bundle
|
35
|
3.0
|
-0.25, +0.25
|
MDB-12/10-7-A
|
7holes 12/10mm Micro Duct Bundle
|
41
|
2.5
|
-0.2, +0.2
|
MDB-12/10-7-B
|
Straightened 7holes 12/10mm Micro Duct Bundle
|
42
|
3.0
|
-0.25 +0.25
|
JMDB-10/8-7
|
Straightened 7holes 10/8mm Micro Duct Bundle
|
37.4
|
3.7
|
-0.3, +0.3
|
JMDB-12/10-7
|
Straightened 7holes 12/10mm Micro Duct Bundle
|
45
|
4.5
|
-0.3 +0.3
|
JMDB-12/10-2
|
2holes 12/10mm Tube Bundle
|
32*22
|
4.5
|
-0.3, +0.3
|
Picture 4:Type and Dimension Deviation of Micro Duct Bundle
Note:
TB/ JTB Micro Duct Bundle or Straightened Micro Duct Bundle
HDPE Micro Duct
Microtubule Cluster Pipe, Microtubule Cluster Tube,Plastic Microtubule Cluster Pipe
ZHEJIANG BOYA COMTECH CO.,LTD , http://www.zjbytx.com